Hydraulic presses
P6320B
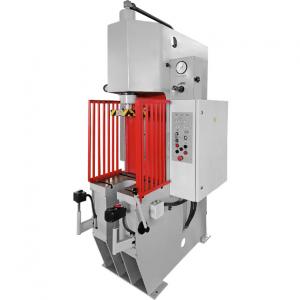
P6324B
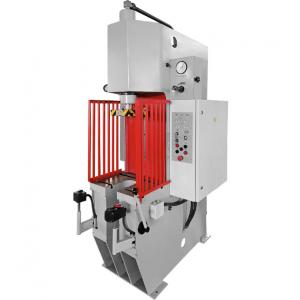
P6326B
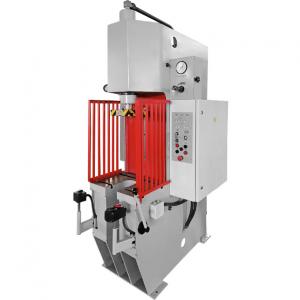
P6328B
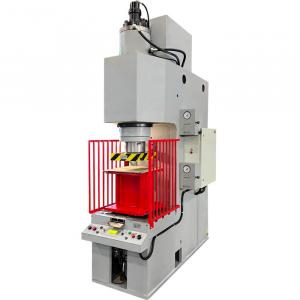
P6330B
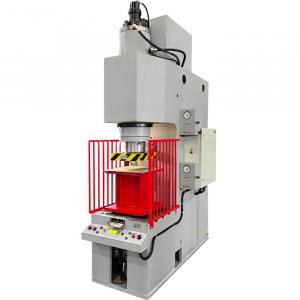
P6332B
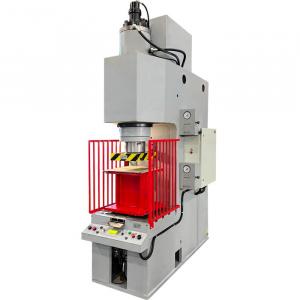
P6334B
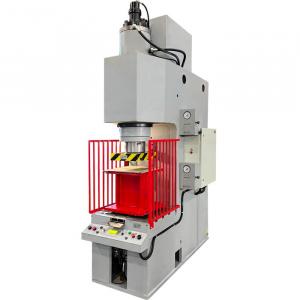
Correct table
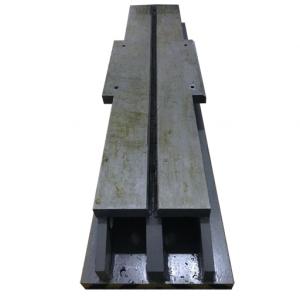
Hydropushion
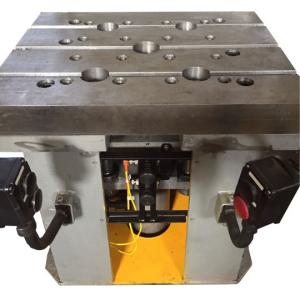
DE2428, DG2428
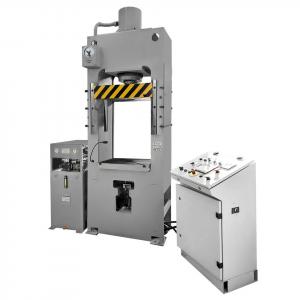
DE2430, DG2430
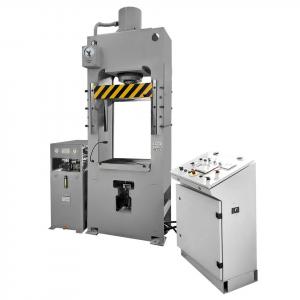
DE2432, DG2432
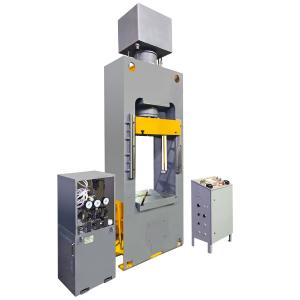
DE2434, DG2434
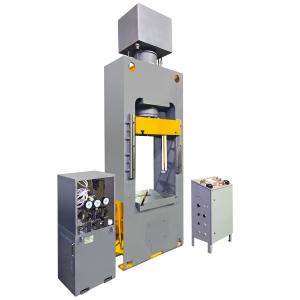
DE2436, DG2436
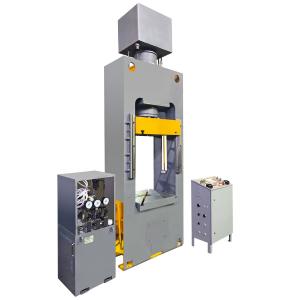
Hydraulic press models P6320B, P6324B, P6326B, P6328B, P6330B, P6332B, P6334B with a force from 100 kN (10 tf) to 2500 kN (250 tf) is used depending on production tasks for straightening and pressing operations. The press has a C-shaped frame configuration. To expand the technological capabilities when performing drawing and stamping operations, it is recommended to equip the press with a hydraulic cushion and a straightening table.
Hydraulic press models DE / DG2428, DE / DG2430, DE / DG2432, DE / DG2434, DE / DG2436 are designed to manufacture products from thin sheet metal, various non-explosive materials and plastics in rubber molds using direct (compression) and transfer (plastic injection molding) pressing. The operation can be carried out with heating using heating plates or without them.
The hydraulic press of the above models differs in the design of the hydraulic units and electrical control cabinets depending on the agreed technical specifications.
Operating procedure of the DE/DG series press design
The press bed has a frame-type configuration. The base and the upper crossbar are presented in the form of two plates with cutouts for the working space, welded into a single whole using side steel plates.
The working part of the table has a welded structure. The upper plane of the table contains longitudinal or transverse grooves for fastening heating plates or a mold. In the center of the table there is a hole for the ejector, and on the sides, depending on the version, there are holes for installing lifting cylinders.
The upper crossbar is a welded rectangular part. Depending on the technological tasks, the main cylinder with or without a filling tank is installed on the plates of the upper crossbar.
The slider has a welded or cast design. With the help of linings, it moves along adjustable wedge guides of the press bed. The lower plane of the slider has grooves for fastening heating plates and equipment in the form of press molds.
Hydraulic cylinders: the main and lifting mechanisms - have a piston or plunger design. The ejector in the standard configuration is only of the piston type.
For reinstallation of molds, the press can be equipped with a special movable table upon request.
The working area is closed with a removable fence.
The press supports two operating modes: setup and semi-automatic.
Operating procedure of the P63 series press design
The press has a C-shaped configuration. The table base and the upper base of the hydraulic cylinder are connected into a rigid structure by two C-shaped and a frontal sheet by welding. The sheet thickness is calculated based on the press force and cylinder reach.
The table is welded. A stamp plate made of structural steel is installed on it. The upper plane of the plate has longitudinal grooves for fastening the tooling. The plate has holes for installing a hydraulic cushion.
The upper base is a rectangular welded part. The main cylinder is installed on it. The hydraulic equipment with a tank is placed in the U-shaped internal cavity of the press.
The slider is located at the bottom of the cylinder, has a central hole and T-shaped grooves for installing the tooling.
Hydraulic cylinders: the main and the hydraulic cushion cylinder can be of piston or plunger type.
The hydraulic cushion is a piston type cylinder. There is a hole on the upper end of the rod for connecting the unit to the ejection system. The under-die plate has holes for installing counters.
The working area of the press is closed with a removable fence.
The press allows operation in three modes: setup, working and semi-automatic. In semi-automatic mode, it can work with and without pre-pressing, with and without a hydraulic cushion.
The lubrication system of hydraulic presses is as follows. Cylinders, as the main hydraulic control components, are lubricated with a working fluid - oil. The rest - manually using a lever-plunger pump.
The operation of the hydraulic press is configured by programming the controller according to the manufacturing technology of the parts. The press is controlled by the operator using a touch panel.